In an industrial park in Austin, there is a building without any signs. A group of researchers study a black technology in the building. Inside the transparent large glass enclosure, the robotic arm can move quickly and accurately on the conveyor belt left and right. Several technicians in blue lab coats, goggles and gloves watched the tumbling movement of an arm in the thick fog.
The fog is caused by the extreme cold indoors, and the indoor temperature can drop to minus 112 degrees. The loud mechanical impact broke the low buzzing sound of the machine when it was running, and gave out a uniform impact.
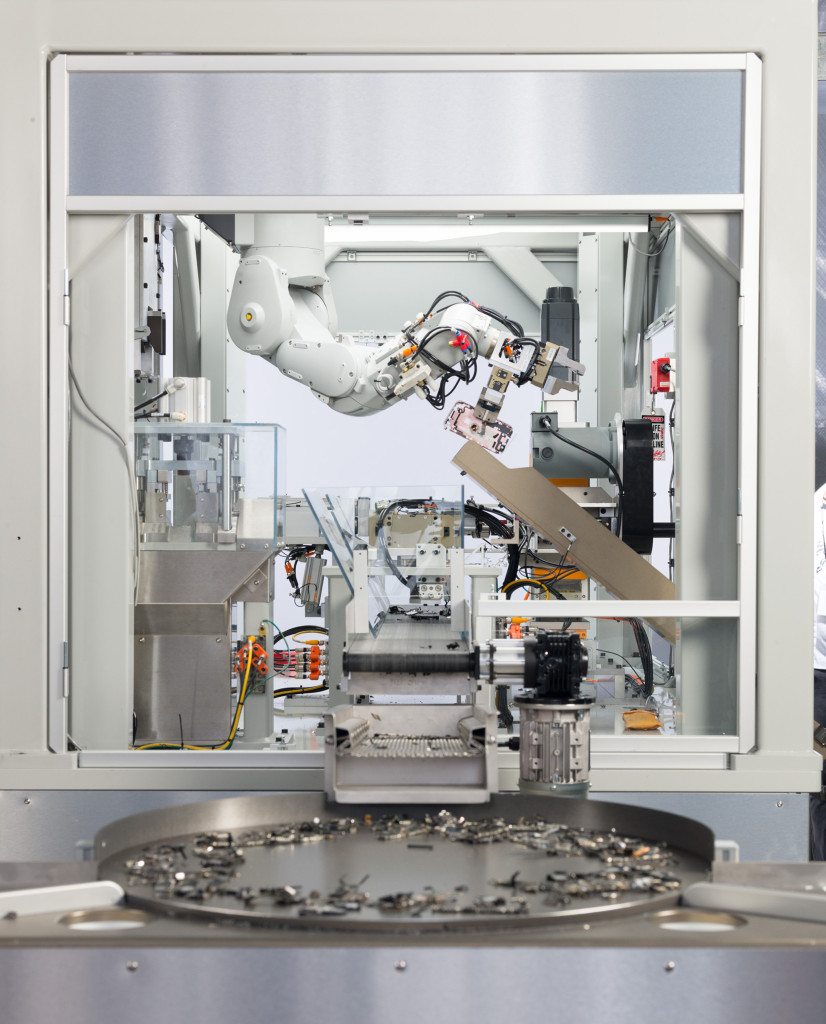
When the Daisy robot debuted last year, it was able to disassemble 15 different iPhone models (starting with iPhone 5) at a rate of 200 units per hour. Since April of this year, 9 million iPhones have been collected through Apple’s trade-in program. This machine in the Austin laboratory and another machine in the Netherlands, together, are processing approximately 1 million of them. (Most of the others enter the refurbishment and resale process). Traditional e-waste recycling facilities are not as sophisticated as Daisy. Most factories rely on bulky machines to crush the products and then pour the finished products into containers of mixed particles. As a result, these mixed streams are more difficult to recycle, and a large number of elements are discarded in the process.
Lisa Jackson, Apple's vice president of environmental, policy and social initiatives, said: "We spent a lot of time on this project to realize the recycling of equipment. Daisy ensured that we have an effective way to disassemble the product's system. "Daisy not only represents a breakthrough in electronic recycling-robots disassemble electronic devices piece by piece-but also represents the vision of minimizing environmental impact.
Apple has always been proud of green certification, for example, a large part of its supply chain is driven by renewable energy. Now it turns its attention to an equally thorny issue: the rapidly growing and often toxic fragments of discarded electronic equipment. How to manage e-waste is becoming an increasingly complex issue. According to the Global e-waste Monitor (Global e-waste Monitor) data, in 2016, 44 million tons of e-waste were generated globally, equivalent to the height of 4,500 Eiffel Towers. Callie Babbitt, associate professor at the Golisano Institute for Sustainable Development at the Rochester Institute of Technology, pointed out: “As companies launch more fashionable and smaller products, the total amount of e-waste In fact, it is decreasing. But a new problem is emerging. The products we use now rely on more and more complex mixtures of rare earth materials and precious metals. As companies launch new products faster and faster, automation systems may have difficulty keeping up Market demand."
Apple refuses to estimate how much its products turn into e-waste. The company sold 217.7 million iPhones last year, an average of about 0.15 kg each. This means that Apple has invested more than 30,000 tons into global households through mobile phones alone. If consumers have better choices, some of these electronic materials will be discarded and become hazardous waste that pollutes the earth.
In 2017, Apple announced a crazy-sounding goal: to achieve that all products ultimately use recyclable or renewable materials, and only use such materials. Apple did not say when this goal will be achieved. However, the Material Recovery Lab, which opened in April this year, is part of the ongoing process, and the company is working hard to turn the experiment into reality. It lists the materials used in 14 products and hopes to eventually recycle them completely.
One of the more critical ones is plastic, which takes hundreds of years to decompose. When it corrodes, it releases harmful toxins, posing a threat to plants, animals, and ecology. There is also lithium. Rechargeable batteries contain lithium. Mining lithium will cause serious damage to the environment. With the help of Daisy, Apple has recyclable these 14 materials. At present, tin and aluminum in new products such as MacBook Air have been completely recycled. Apple not only wants to improve its own production process, but also wants to improve the recycling of materials throughout the industry. Part of its Austin factory is dedicated to extensive research and development of electronic waste recycling, hoping to innovate equipment that recycles more materials and improve the consumer technology supply chain.
To achieve this goal, it is a long road for Apple and requires the joint efforts of many people in the industry. Even some Apple executives do not believe this is feasible, but with the efforts of engineers and team members, they have found that full recovery is not only possible, but also essential. "If we don't want the ultimate fate of Apple products to be earth trash, we can only spend time researching, spending money to invest, ensuring the long-term use of hardware, reusing materials, and changing the insurmountable problems."